From Paper Binder to Connected Factory: the Success Story of Arquus with Inetum.
From Paper Binder to Connected Factory: the Success Story of Arquus with Inetum.
Customer Success Stories
By supporting Arquus in its digital transformation, Inetum has enabled the manufacturer to improve manufacturing quality and meet production deadlines.
Creation date :
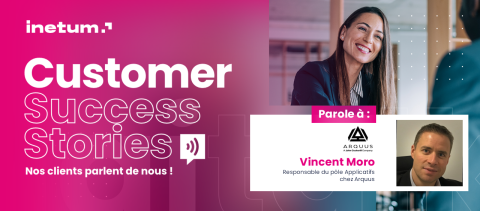
How to move from a 500 page paper-based system to a fully digitized one? Since 2019, Inetum has been assisting Arquus in its digital transformation, revolutionizing production methods and simultaneously improving quality and manufacturing speed in the production of armored vehicles. An exemplary case study of industrial digitalization in the defense sector.
Just four years ago, in the factories of Arquus, (a French manufacturer of armored vehicles) operators were assembling vehicles by consulting 500-page paper manuals. If any modification occurred, the entire document had to be reprinted. Today, these same operators use touch screens that guide them through the operations step by step. This digital revolution was led in partnership with Inetum, an expert in industrial digital transformation.
Digital Transformation: A Strategic Challenge
"Integrating digital technology into the factory is very recent, and even more so in the context of Arquus," explained Vincent Moro, head of the Applications division at Arquus. “This transformation addresses a vital dual objective: improving manufacturing quality and meeting production timelines, two imperatives that previously seemed contradictory.”
The collaboration between Arquus and Inetum began in 2019 when the manufacturer sought Inetum's expertise to support its PLM (Product Lifecycle Management) project. Given the complexity of the challenge, the relationship has intensified, and today between 20 and 30 consultants from Inetum are involved in various areas.
Operators Guided in a Traceable System
The most visible change concerns daily life in the workshops. With the ongoing implementation of an MES (Manufacturing Execution System) based on PTC's ThingWorx solution, Arquus will completely transform its production methods. In January 2024, Inetum was selected as the integrator to deploy this solution.
"Practically, at each workstation on the production line, operators have a screen with step-by-step instructions. They have access to documentation and all necessary assistance," explained Vincent Moro. At each step, the operator can validate their action or report a problem, allowing real-time tracking.
This system also ensures critical traceability. When an operator installs a component like an engine, they scan its serial number. All this information is fed back into the PLM. A valuable feature that will be useful throughout the product's lifespan, in a sector where some vehicles designed in the 1970s are still in service.
The "Golden Triangle" and a Relationship of Trust
It is in the cement between all these bricks that the magic happens at Arquus - What Vincent Moro calls the "golden triangle": PLM, ERP, MES. "An ERP (integrated management software that coordinates resources and planning) functions more on an hourly or daily rhythm. An MES functions to the minute or even quicker," he explained. The PLM, for its part, ensures "digital continuity" by documenting the design elements.
Inetum is involved at different levels: as AMOA on the PLM project, as an integrator for the MES, and as technical assistance on various subjects. What stands out from the four years of collaboration is above all a relationship based on responsiveness and trust. "There is responsiveness, and our needs are listened to," said Vincent Moro. Jean-Richard Venn, who heads the Industry 4.0 BU at Inetum, added: "Our goal on these complex subjects is to react quickly and correctly when difficulties need to be addressed."
This collaboration will continue, "for several years, at least two years," assured Vincent Moro. “Projects around augmented and virtual reality are also being studied to go even further in efficiency and allow Arquus to meet its challenges," added Jean-Richard Venn.
In the meantime, Arquus is already reaping the benefits of this transformation. In a defense sector under pressure, where global geopolitical tensions require rapidly adaptable production capacities, the shift from paper to digital is much more than mere modernization—it's a crucial strategic advantage.
The lexicon of Industry 4.0
PLM (Product Lifecycle Management): A system that manages the entire lifecycle of products, from design to maintenance.
MES (Manufacturing Execution System): A computer system that controls and monitors production in real-time in the workshop.
ERP (Enterprise Resource Planning): Integrated management software that coordinates resources and planning.
ThingWorx: An industrial IoT solution developed by PTC, connecting the physical world to the digital world.
AMOA (Assistance to project owner): Actors responsible for interfacing between the client (project owner) and the "technical" provider by facilitating dialogue between the parties to ensure the project's objectives are met.
Contact : Jean-Richard Venn