Aircraft engine manufacturer
Fewer delays at airlines and safer flights thanks to predictive maintenance for aircraft engines via the cloud.
An aircraft that unexpectedly remains grounded, for any reason, is always a setback for an airline.
That is why the world’s second-largest aircraft engine manufacturer offers its customers a proactive form of maintenance: aircraft engines as a service, where customers pay for a functioning engine and its service level agreements (SLAs). To achieve this, the manufacturer utilizes a variety of data-driven cloud solutions, from the Internet of Things (IoT) to artificial intelligence.
“Did you know that at any given moment, between 8,000 and 20,000 commercial aircraft are in the air?” asks Sebastian Stefanowski, Senior Cloud Architect at Inetum East. “Considering that each aircraft carries an estimated 80 passengers on average, that translates to between 640,000 and 1.6 million passengers flying at any given time.”
In 2024, the total volume of flights surpassed 38 million. “That amounts to just over three billion passengers per year,” our Polish cloud expert calculates. This represents a vast number of customers that an airline risks disappointing, or even losing, if it has to unexpectedly ground an aircraft for repairs or maintenance.
Costly downtime
“If engine repair or maintenance is required, you can expect a waiting period of three to four days,” explains Sebastian Stefanowski. “Such an incident not only affects the original flight but also disrupts around twenty other flights and impacts more than 8,000 additional passengers. The total delay caused by such an incident can last nearly five days. And before all flight schedules are fully restored and operations return to normal, it can take up to seven full days.”
Moreover, Sebastian Stefanowski points out the significant financial damage that downtime inflicts on the responsible airline. The total cost of a single such incident amounts to three million dollars or 2.8 million euros. “That’s quite substantial,” he remarks. “It clearly presents opportunities for savings if airlines can devise an effective solution to this problem.”
Continuous quality control
Ultimately, the key to the solution lay with the aircraft engine manufacturer itself. In collaboration with IT partner Inetum, the company developed a new service enabling predictive maintenance: Engine Health Monitoring (EHM). As the name suggests, this service continuously monitors the ‘health’ of aircraft engines, allowing for predictive, i.e., proactive and preventive, maintenance when necessary.
“Using various sensors, the aircraft engine manufacturer can monitor 12,000 aircraft engines around the clock,” explains Sebastian Stefanowski. “This amounts to a total of 14 million flight miles covered by customers each day, generating over five million parameters to measure daily. All this data is processed within an average of three minutes.” The Engine Health Monitoring service is capable of detecting 130 failure modes. “This results in approximately 400 warnings per year, with fewer than 20 being false alarms. Most importantly, in 2016 alone, the aircraft engine manufacturer managed to prevent over 200 million euros in failures for its customers by effectively utilizing this new service.”
Inetum provides advice and support
This new service would not have been possible without the aircraft engine manufacturer’s decision to migrate to the cloud. For its large-scale Azure migration, the company enlisted the expertise of Inetum. “I was the first engineer to advise them on this transition,” recalls Sebastian Stefanowski. Today, the cloud team consists of 120 engineers, each with their own expertise in areas such as data integration, user interface, business intelligence (BI), and more.
Over the past ten years, more than seventy different cloud environments have been set up, most of them temporary to save costs, and more than thirty exclusively for automated release testing. “Through this collaboration, we have gained extensive hands-on experience in the Azure environment. Additionally, we work continuously with the aircraft engine manufacturer to drive constant improvements. We not only aim to enhance existing techniques but also focus on developing new methods for detecting failure modes.”
Product-as-a-Service
Investments in the cloud have enabled the development of data-driven solutions in new technology domains such as IoT, big data, and AI. “Data, particularly the massive streams generated by IoT, forms the foundation for the development of intelligent, AI-driven equipment. In this sense, data is truly the new gold.” As mentioned earlier, investments in IoT technology and big data analytics have not only resulted in significant cost savings but also facilitated a fundamental business transformation. They have enabled the aircraft engine manufacturer to optimize its business operations and fully transition to a Product-as-a-Service model.
“In the past, customers paid for regular engine maintenance at fixed intervals. Any additional unforeseen maintenance required extra payment,” explains Sebastian Stefanowski. “Today, airlines pay a fixed annual fee to the aircraft engine manufacturer for the proactive assessment and timely resolution of any potential engine issues. This annual fee is based on the total flight hours of their engines in the past year. If their engines fly more, both the airlines and the aircraft engine manufacturer benefit. As an added bonus, this shift in the business model also enhances passenger safety.”
More information?
Would you like to discuss how to leverage the cloud as a driver for business and innovation? Contact us via info.belgium@inetum.com. For a brief overview of our approach, click here.
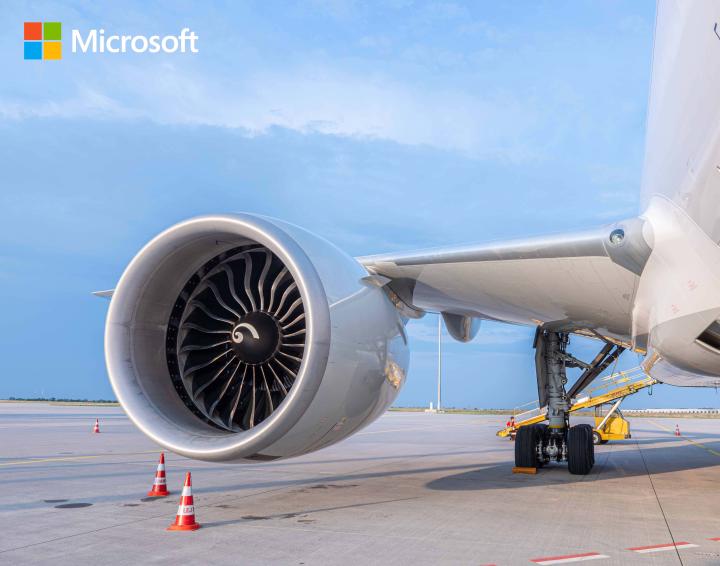